Resource-preserving production by means of robot handling
Mechanik-Moduls GmbH from Forstinning-Moos near Munich has been involved in the machining of high-precision workpieces since 1990 – from prototype to large-scale production. Among others, customers in the medical, semiconductor and aerospace sectors have put their trust in the quality-oriented work of the 20 specialist employees. In addition to 3D printing and component assembly, the range of services provided by Mechanik-Moduls primarily includes CNC milling and turning. As a result of regular investments in modern cutting technologies, the company is now using five machine tools from DMG MORI, which are mainly automated. The company’s most recent purchases include two DMU 50 with Robo2Go Milling, which Mechanik-Moduls financed through DMG MORI Finance as a rental purchase because of the attractive conditions that were available.
Consistent quality and process optimization using automation
“As a manufacturing service provider, we are faced with the challenge of providing consistent quality and reacting flexibly to the respective order situation,” explains Daniel Thoma, who manages Mechanik-Moduls together with his brother Dominik. The young team impresses with its technical expertise, which is incorporated during the development of new customer components, as Dominik Thoma explains: “With prototypes and in the optimization of existing components, well-thought-out machining processes help to speed up production and make them more economical.” The machine tool automation plays an important part in this process optimization.
Mechanik-Moduls installed the first automated DMG MORI machines in 2017: a SPRINT 32|8 with a bar loader and a MILLTAP 700 with integrated WH 3 for autonomous workpiece handling. “Both of the machines are used to machine recurring series,” says Daniel Thoma. “The automation solutions allow us to work to our full capacity, even during unmanned night shifts.” The employees themselves only work single shifts. It was obvious to the two managing directors that future purchases would also have to be automated. A DMU 50 with Robo2Go Milling therefore followed in 2021.
“Our two MILLATP 700 systems have proven that 5-axis machining is a crucial productivity factor,” says Dominik Thoma, assessing the investments. The DMU 50 was a logical step, adds Daniel Thoma. “The 5-axis simultaneous machining center is more stable, which allows us to perform machining that is more efficient and precise.” The compact design including Robo2Go Milling has also made it possible to extend the tool magazine to 60 locations. “This is more than sufficient, particularly for automated operation.” The Machine Protection Control 2.0 technology cycle, for example, is equally as valuable in autonomous manufacturing. “In this way, we can avoid collisions and tool breakage in an absolutely reliable way.” Consistent use is made of these and other digitalization features in order to optimize processes even further. “my DMG MORI is a good example, since it speeds up our service processes significantly, and makes them completely transparent,” says Daniel Thoma.
Fast and flexible order planning thanks to Robo2Go Milling
DMG MORI has been trying out Robo2Go on the market for several years – initially as Robo2Go Turning on lathes. “The Robo2Go Milling for machining centers was brand new when we placed the order,” recalls Dominik Thoma. It is said to have been the first of its kind in Bavaria. The compact automation solution was an exact fit for the part of the building which was intended for this purpose, since when it has mainly machined workpieces for the medical sector. “There are two versions of a component that Robo2Go Milling handles from a magazine,” says Dominik Thoma, describing the process. However, other orders can also be integrated quickly and flexibly. Daniel Thoma sees a clear advantage here: “Because we often have to react at short notice to fulfill delivery deadlines.” Impressed with the DMU 50 with Robo2Go Milling, Mechanik-Moduls purchased a second, identical solution in 2023 to increase its capacity. Dominik Thoma is satisfied with the decision: “This allows us to also machine the rear of the medical components at the same time.
Convenient rental purchase with the support of DMG MORI Finance
Mechanik-Moduls has made repeated investments in machine tool equipment from DMG MORI with the support of DMG MORI Finance right from the beginning. “This makes us more independent of our main bank and the conditions are comparable,” says Dominik Thoma, explaining the financing. DMG MORI Finance provides leasing, rental or hire-purchase – the latter was chosen by Mechanik-Moduls – and provides the possibility of reduced initial installments in order to preserve liquidity. This allows the machine to generate additional profit early on. Annual fee-free special repayments are also possible.
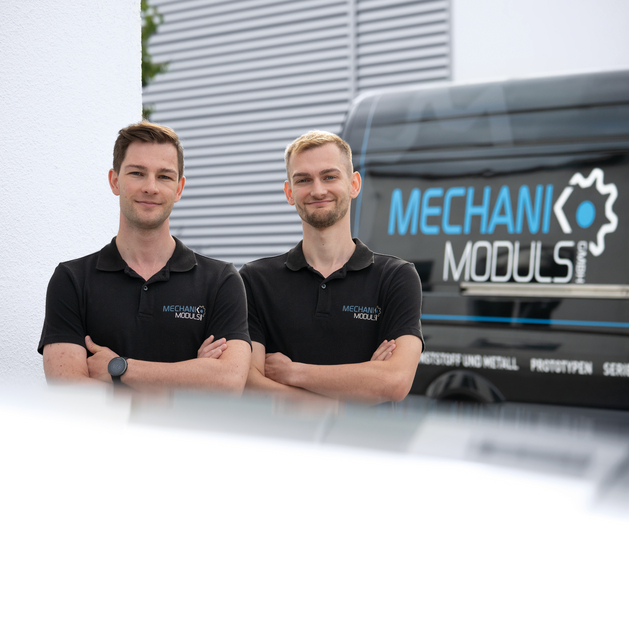
Future-proof modernization of the machinery
Because of the company’s positive experience with automated machine tools from DMG MORI and the financing options, Mechanik-Moduls would like to keep the good cooperation going. As soon as older machines need to be replaced, DMG MORI’s wide range of products will be examined for future-proof manufacturing solutions. Daniel Thoma is already looking ahead: “Automation solutions will be an important component, because they will allow us to maximize our capacity utilization and mitigate the shortage of skilled workers.”
Mechanik-Moduls GmbH
Römerstraße 10
85661 Forstinning, Germany
www.mechanik-moduls.de