Precision machining for cuttingedge research
The Max Planck Institute of Quantum Optics (MPQ) in Garching near Munich has its origins in a project group for laser research, which was founded in 1976 at the Max Planck Institute for Plasma Physics. It was awarded the status of a separate institute five years later.
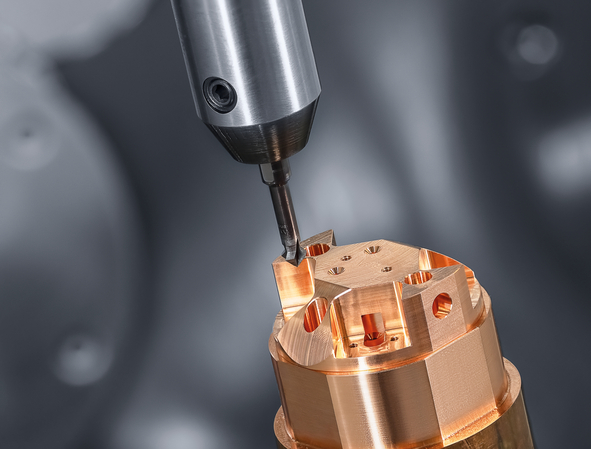
With four departments in different areas of laser development and quantum physics, the MPQ has been researching the interaction of light with quantum systems ever since. The departments of the institute deal with quantum matter at extremely low temperatures, the fundamentals of quantum optics and attosecond physics. It also focuses on experiments with individual quantum particles and information. The respective laboratories use complex, high-precision equipment, which is built with the support of the in-house workshop. 15 specialists manufacture precision components with the most demanding geometries on DMG MORI machine tools. The machine shop includes a DMU 40, a DMU 50 and a DMU 65 monoBLOCK for 5-axis simultaneous machining. There is also a CLX 450 for turning operations.
Two Nobel Prizes in Physics
Research at the Max Planck Institute of Quantum Optics provides physicists with ever deeper insights into the microcosm. The results are so groundbreaking that two Nobel Prizes in Physics have already been awarded to Garching employees – the first in 2005 to Professor Theodor W. Hänsch for the development of laser-based precision spectroscopy. This technology can be used to determine the color of light from atoms and molecules with extreme precision. In this way, frequencies can be measured with an uncertainty of a few millionths of a billionth of a hertz. Professor Theodor W. Hänsch researches high-precision laser spectroscopy of hydrogen and similar elements at the MPQ in the Emeritus Group for Laser Spectroscopy.
The Nobel Prize was awarded to Professor Ferenc Krausz in 2023. At the beginning of the century, he and his team succeeded in isolating a single X-ray pulse with a duration of 650 attoseconds. One attosecond corresponds to a billionth of a billionth of a second. This corresponds to the ratio of one second to the age of the universe. The interaction of electrons with each other or with light in matter also takes place on this unimaginably small time scale. It therefore requires extremely short exposure times to observe or control electrons at the atomic level in real time. This is exactly where attosecond physics can help. Professor Ferenc Krausz sees a practical benefit for medicine. After all, electron movements also play a role in biological systems. With this research, infrared, X-ray, and particle sources driven by femtosecond laser light are being developed and used for the early diagnosis and treatment of cancer.
5-axis simultaneous machining for complex, high-precision components
The high standards of research at the MPQ are also reflected in the in-house workshop. “Our laboratories need very special, high-precision optical instruments to carry out their experiments”, explains Michael Rogg, who has been at the institute since 1986 and head of the workshop for 13 years. “Engineers design device components according to the specifications of the researchers, which we manufacture to the required quality and accuracy.” For this task, the workshop team is equipped with modern 5-axis simultaneous machining centers from DMG MORI. The most recent acquisition was a DMU 40 in December 2023. “The stability of the machines and their extensive cooling systems allow precise machining of the often complex geometries,” says Michael Rogg.
Complexity and precision on the one hand and the wide variety of materials on the other are what characterize the orders in the MPQ workshop. “As many experiments are carried out in a vacuum, stainless steel components are common, but aluminum, copper alloys or special plastics are also used due to their individual properties,” comments Michael Rogg on the wide range of materials. The challenge lies in taking the behavior of the diverse materials into account in the machining process. Another challenge is the individual machining strategies. The mostly small workpieces can be very delicate and this in turn requires machining that is as stress-free as possible. Michael Rogg mentions tolerances that are in the range of a few micrometers in extreme cases: “Even a thread cutter can cause unwanted deformations.” That is why an M1 thread has already been milled on the DMU 65 monoBLOCK and not cut.
Motivated specialists with a willingness to learn
In production, one person is always responsible for the entire component – from programming through to final quality control. This is how Michael Rogg explains the high demand for good personnel: “Unlike in industry, profitability is only a secondary concern in research. What counts first and foremost is the perfect result. This means that we are looking for particularly motivated specialists and young people that are willing to learn.” The MPQ is currently preparing three trainees for this exciting job.
Longstanding partner in machining
In cooperation with research institutes, universities and vocational schools, the DMG MORI Academy is responsible for equipping the workshops. It is well aware of the requirements there and knows the differences to industry. In the case of MPQ, Michael Rogg can look back on many years of cooperation with the DMG MORI Academy: “We have been using CNC technology from DMG MORI for decades. With new purchases, we can be sure that we always receive manufacturing solutions that meet our stringent requirements.”
Max-Planck-Institut für Quantenoptik
Hans-Kopfermann-Straße 1
85748 Garching bei München
www.mpq.mpg.de